Tiefbohren-ウィキペディア
ディープドリル また Tieflochbohren 掘削深度を備えた掘削の特別な処理であり、直径よりも多くの倍の掘削です。
VDIガイドライン3210の意味では、深い掘削プロセスは、穴の生産と処理に製造プロセスを費やしています。その直径はd = 0.2….2000 mmの間で、その穴の深さは直径のトリプルよりも一般的です。 [初め] 小さい掘削直径の場合、長さと直径比L/d≤100の場合、特別な場合では、l/d = 900までさえ達成できます。 [2] [3] [4] 大きな直径の場合、L/D比は通常、機械の移動とその床の長さによって制限されます。 [5] [4]

深い掘削は、掘削プロセスと大量の高圧下での掘削直径とは、透けた潤滑剤をスパンポイントに汲み上げる必要があるという点で、短い掘削とは異なります。これにより、ワークピースとツールカットエッジの間の効果領域の良好な冷却と同時潤滑が必要になり、他方のワークとガイドストリップが必要です。さらに、冷却潤滑剤はアクティブゾーンから一定のチップ除去につながり、時間を増やし、表面の損傷と時間を抑える切断カッターが余計になります。 [初め] 深い穴を生成するために、2つの異なるタイプのツールが区別されます。一方で、非対称の鋭い構造を持つこれらのツールはそうです。これには、ディープドリルの挿入による掘削、シングルチューブシステム(BTAディープドリル)に従ってツールを掘削すること、および「クラシック」ディープドリルプロセスと呼ばれるダブルパイプシステム(Ejector Deep Drilling)に従ってツールを使用したディープドリルが含まれます。一方、これらは対称的に配置されたメインカットを備えたツールタイプであり、スパイラルディープドリルと2つのリップディープドリルに使用されます。これは、実装する掘削深度のためにディープドリルプロセスに割り当てることもできます。
言及されたツールタイプは、実現可能な直径範囲、達成可能なL/D条件、表面の品質、およびその生産性の点で異なります。対称ツールでは、d = 0.2…32 mmの小さな直径の範囲でのみ、最大L/d = 85のL/D比の穴を生成できます。L/D = 30のL/D比の標準は、非対称ツールで、通常はD = 0.5の直径範囲の領域では、通常はd = 0.5の領域では、測定値が制限される可能性があります。図では、通常のアプリケーションの直径を備えた選択された深い掘削プロセスが示されており、深い掘削プロセスがすべての直径領域で競合していないことが明らかです。小さな直径範囲の「クラシック」ディープドリルツールと比較して対称的に構築されたツールの利点は、Fの前に著しく高い可能性があることです。 [初め] [6] [7] [8]
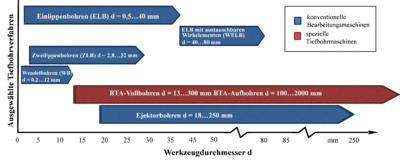
L/D比が高いことに加えて、「クラシック」ディープドリルプロセスは、HSSウェンデルドリルを使用した掘削プロセスと比較して、表面品質が高い生産性が高いことを特徴としています。高いボアの品質は、高い表面の品質、低直径の偏差と幾何学的精度で特徴付けられます。これらの深い掘削ツールの非対称構造は、良好な表面の品質にとって重要です。いくつかの例外を除いて、「クラシック」ディープドリルプロセス、肘の掘削、BTA掘削、エジェクター掘削のツールは劇的であり、マイナーカッター(円形粉砕チャンバー)とガイドストリップがあります。過程で、この建設的な状況は、ガイドストリップを介してボアウォールに移動し、したがってワークピース壁に移します。ツールヘッド上の特定の電源コンポーネントの場合、「閉じた」力が生じ、作成されたばかりの穴のツールをサポートし、そのために導きます。したがって、深い掘削における力の経過は、従来の掘削とは異なります。この掘削では、力がツールによって大きく吸収され、したがって機械の紡錘体によって吸収されます。深い掘削の強度の強度の偏りのために、一方で穴の中のドリルになり、したがって中央の中心が比較的低く、一方では、穴の壁とガイドストリップの間の「サポート」を通じて形成プロセスが行われ、穴の壁を滑らかにします(理想的なケース)。切断によって引き起こされる表面の粗さは、ガイドストリップの下での形成プロセスによって約70%減少し、サポートの割合が高くなります。 [9] これは、9からIT 7へのボア耐性により、非常に高い表面の品質を達成できることを意味します。多くの場合、配信手順を削減するか、完全に省略することができます。もう1つの利点は、クロスホールを掘削して掘削する際の低い尾根層です。 [初め] 表面の品質が高いと同時に、従来の深い掘削プロセスの使用は、掘削の深さが低い場合でも経済的になる可能性があります。 [5] [十]
必死の掘削 [ 編集 | ソーステキストを編集します ]

彫刻の深い掘削は、通常、d = 0.5…40 mmの直径範囲の穴の生産に使用されます。現在、このアプリケーションの領域は、クーラント潤滑剤チャネルの製造技術的実装と、ツールの直径の減少による研削技術生産の課題の増加により、下方に制限されています。上限は、代替の深い掘削プロセスのより経済的な使用に起因します。 [初め] [12番目] 腎臓の形状または2つの円形冷却チャネルを介した内部冷却潤滑剤供給は、結実の深い掘削の特徴です。チップ潤滑剤混合物は、いわゆるseeckeであるツール上のV字型の縦溝で実行されます。クーラント潤滑剤質量電流は、チップを除去するための唯一の輸送メカニズムです。このため、直径依存の高圧クーラー供給が必要です。天井ツールの一般的な構造は、掘削ヘッド、シャフト、クランプスリーブの3つの部分に分かれています。通常、掘削ヘッドは、硬いはんだ付けによってシャフトとともに追加されます。クランプスリーブは、ツールのクランプ要素であり、ツールの摂取量、したがって工作機械のインターフェイスを形成します。ツールの直径と高パフォーマンスツールが小さい場合、フルハードの金属ツールがよく使用されます。これらのより強力なツールを使用すると、掘削ヘッドとシャフトは硬い金属棒でできています。掘削ヘッドは、主にISO Recess Group K 10からK 20から硬い金属で作られており、必要に応じてコーティングされています。 PKD、セルメット、セラミック、または高速作業鋼も特別な用途でも使用されています。 [初め] 掘削ヘッドのジオメトリは、現在の処理状況に応じて選択されます。この点で、さまざまな切断エッジとガイドストリップのサイズが区別されます。インレットドリル用の通常の標準接続により、メインの最先端は外部と内部の切断エッジに分割されます。これは、調整角度が異なるため、穴の直径によって異なります。円周形の選択も来ます、つまりH.ガイドの数と配置は、フレームドリルの程度までストリップします。スパイラルドリルによる従来の掘削と比較して、摩擦掘削は、その適合性と大きな長さと直径の比率での高いプロセスの信頼性によって特徴付けられます。さらに、掘削掘削は比較的高いボアの品質に達し、ポスト処理の節約を可能にする可能性があります。 [初め]
ツール


画像に見られるように、フレームドリルは、ツール録音、シャフト、および掘削ヘッドを形成するピース(主に硬い金属)で構成されています。構造の観点から、一般的に、シャフトは掘削ヘッドよりも1/10 mmから1 mmの小さい数で保持されていると言えます。また、1/4のシャフト表面が自由に作業していることもわかります。この表面では、クーラントストリームのためにチップが穴からすすいです。切断ヘッド自体には、マシンの機械軸のスパイラルドリルとは異なり、ドリルがリードしているグラインドガイドエリアがあります。
実際の最先端は、ドリルの中央の上の先端です。これは、ドリルが退屈するために材料を一方的に擦り合うことを意味します。結果として得られる最先端のチップは、少なくとも1つ、約10 mmドリルの直径、2つ以上のチャネル、およびクーラントと外側から、同時にシャフトの自由を編集現場から洗浄します。
BTAディープドリル [ 編集 | ソーステキストを編集します ]

チップと掘削面との低いねじれモーメントなどのフリンジ深い掘削の欠点は、これらの問題が回避され、良好な特性を備えた変化した深い掘削プロセスを開発する動機でした。 1950年代初頭にBTA手順という名前を受け取った新しい深い掘削プロセスが1940年頃に開発されました。
BTAは、現在清算されたブレーメン会社GebrüderHellerが支配していた「退屈とトレパニング協会」の略です。彼女のリーダーシップの下で、新しい手続きは、BurgsmüllerとBeisnerの開発との開発に対処するプロセスのために、第二次世界大戦中に作成されました。 Burgsmüllerは、以前に使用した掘削チューブを交換し、交差点でパイプを閉じたもので、ねじれ硬化であり、初めてパイプの内部を通してチップを宣伝しました。 Burgsmüllerは、両刃のツールとエアオイル混合物を使用しました。これは、最小限の潤滑剤で製造するときに使用されています。 Beisnerはツール構造を改善し、クーラントとしてオイルを導入しました。 HM-stocked ELBツールを導入した最初の会社であるHellerは、最先端のコントロールボード星座の特許を取得し、BTAツールにも使用されました。
処理プロセス中に、イラストに見られるように、冷却潤滑剤は、生成された穴と掘削チューブの間のリングギャップによるアクティビティポイントである掘削油供給システム(BOZA)の助けを借りて供給されます。 Bozaは、ワークピースと掘削チューブの間のシールも引き継ぎます。これには、ワークピースに向けられた円錐形の回転ワーク記録があり、高圧でワークピースに押し付けられています。ワークピースは中央にあり、シーリングエリアの接触があります。ほとんどの場合、ボザの背面は詰め物の茂みによって封印されており、掘削パイプガイドの機能も引き継ぎます。掘削ソケットは通常、BOZAに統合されており、BTAプロセスでパイロットボアを使用することはめったにありません。
ツール



ツールに統合された開口部により、チップはオイル電流の助けを借りて消散します。それが、開口部が「スパンマウス」と呼ばれる理由です。チップは、穴と接触せずにこの方法で消散することができます。ツールと掘削チューブの円形の断面により、このプロセスは肘の掘削と比較してより大きなねじれ抵抗トルクを持っています。つまり、非常に高いスパンパワーを達成できます。 BTAプロセスは、d = 6…2000 mmのボア直径に使用されます。産業プロセスでは、約16 mmの領域で使用されます。直径6 mmの直径のBTAドリルを生産する可能性は与えられていますが、まだ既知のアプリケーションはありません。 [13] [13] [14] [十] [11]
Ejector Deep Drilling [ 編集 | ソーステキストを編集します ]


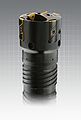
Ejector手順は、d = 18…250 mmの直径範囲で使用されます。これは、使用される掘削ヘッドがBTAツールに建設的に匹敵するBTA手順のバリアントです。唯一の違いは、KSSの屋外オープニングが範囲で開かれたことです。冷却潤滑剤は、掘削チューブとインナーチューブの間のリングルームと交差しているため、2つのチューブプロセスの指定もプロセスに提供されます。既に述べたKSSアウトレットの開口部の側面にある冷却潤滑剤の葉は、掘削ヘッドを洗い流し、チップを生成して内側のチューブに戻ります。クーラント潤滑剤の一部は、リングノズルを介して内側のチューブに直接導かれます。これにより、スパンマウスに負圧(エジェクター効果)が作成され、内側のチューブの逆流が促進されます。システムは、外部高圧ポンプまたは内部KSS供給を介して操作できます。 BTAの手順とは対照的に、逃げる冷却潤滑剤に対するシーリングは必要ありません。エジェクター手順は、従来の旋盤や処理センターでも使用できます。チップを取り外すパイプ断面は、ダブルパイプシステムによって縮小されるため、切断出力はBTAプロセスよりも低くなります。このため、通常、エジェクターの深い掘削中に切断速度が低くなります。さらに、剛性の低下は、ツアー特性の悪化に関連しています(IT9からIT11)。 [初め] [15] [14] [16]
手順の実装の前提条件は、旋盤または加工センターのスピンドルのリボルバー消費に使用される接続ピースの使用です。この接続ピースを通じて、KSSは、接続されたポンプユニットによって、内側と外側のチューブの間のリングギャップに向けられます。この関数を有効にするには、2つの異なるバージョンが可能です。処理センターの場合、旋盤には回転する非回転接続ピースが必要です。機械加工マシンを選択する際には、関連するスペース要件を考慮する必要があります。
ツール
Ejector Deep Drillingのツールの構造は、BTAディープドリルツールの構造とほぼ同じです。追加のKSSアウトレットの開口部は、図に示されています。
古典的な深い掘削プロセスに加えて、深い穴の最終処理のための他のさまざまな手順があります。これらは、表面の品質に関して再加工することも、複雑な輪郭および非発色の輪郭を処理するための基礎として機能します。
内部プロファイル作成 [ 編集 | ソーステキストを編集します ]
さまざまな理由で、深い穴のあるコンポーネントがあり、その内部の輪郭は回転するが、均一に円筒形ではない。このようなコンポーネントは、スピンキャストフォームや押出機のシンダーの円錐形の穴、プロペラ波やシャーシなどのアンダーカットなど、アンダーカットのない輪郭のない場合があります。
このようなチャンバーバッグを生産するには、高品質の事前掘削が必要です。放射状に拡張可能な切削工具がNC軸を介して制御され、深い掘削機のNCボアスライドに接続されている場合、輪郭の長さ全体にわたって穴の輪郭を生成することがほとんど可能です。
最先端の位置は、軸方向のシフトによって変更できます。 B.内側の引き出しを使用します。さらに、ガイドパッドは油圧で調整することもできます。ガイドホールは、最初の切断ステップの後、SOコールされた長いチャンバー処置ですでに完全に回転していたため、管理パッドも大きなチャンバーをサポートするために放射状に調整できる必要があります。この方法に代わるものとして、このツールは事前にドリルされたガイドホールにのみ存在するため、SO -Calcaled Short Chamber Procedureは拡張可能な管理パッドを必要としません。 [17] [18] [19] [20]
ピールとスムーズローラー [ 編集 | ソーステキストを編集します ]
皮をむき、掘削直径の丸みと寸法精度が向上します。アンダーグラウンドゾーンの近くで開いた表面プロファイルが作成されます。これは、滑らかなローラーやホーンなどのその後の処理プロセスに特に適しています。油圧シリンダーとシリンダーソケットを処理する領域では、皮をむき、滑らかなローラーが関連する製造プロセスと見なされますが、純粋に切断され、形成されたコンポーネントもあります。この理由は、皮を組み合わせた滑らかなローリングツールを幅広く使用しているためです。 [21] [22] [23] [24] [25] [26] [27] [28]
抜本的なこすり [ 編集 | ソーステキストを編集します ]
表面の品質と穴の寸法精度を向上させる別の処理プロセスは、クラッシュの使用です。グリングは、事前に漂う穴の下限であり、それによりツールはガイドパッドによってサポートされています。したがって、これらの摩擦のツールジオメトリは、フリンジドリルに非常に似ています。小さな切断深さで恐ろしい掘削の違いは、周囲にほとんど欠けている円周、フライス車と低いクーラントの量と圧力に平行な長い側面の刃先です。 [29] [30]


ディープ掘削プロセスまたはディープドリル方法を使用して処理するために、深い掘削機は主に標準(多目的)または特別なマシンとして使用されます。
掘削深度が低い穴(最大40×D)の製造では、編集センターでフレームドリルが使用されています。
イジェクターの掘削は、主に従来の工作機械で使用されます。ディープドリルの生産性は高いため、比較的強力なマシンのみが使用されます。原則として、KSSシステムが必要であり、KSSは(他の掘削プロセスと比較して)より高い圧力での平均を超える大量流量を提供します。
深い掘削システムとして、このグループは、深い掘削機とKSSの準備とタップ処理のための他の周辺機器を備えたKSSタンクで構成されることを理解しています。
イジェクター掘削プロセスは、従来の工作機械で使用するための深い掘削技術として開発されました。フリンジディープドリルの使用は、シリーズ生産における機械加工センターで特に一般的です。
右側に見られるのは、通常のディープドリルマシンのスキームです。 [初め]
- VDI 3208:フルーツドリルによる深い掘削
- VDI 3209:冷却潤滑剤の外部給餌による深い掘削(BTAおよび同様の方法)
- VDI 3209:シート2ディープドリル。穴の剥離と滑らかなローリングのための値をガイドします
- VDI 3210:シート1ディープドリルプロセス
- VDI 3211:機械加工センターでの深い掘削
- VDI 3212:シングルスピンドルおよびマルチスパンドルディープドリルマシンの受け入れ条件
- ↑ a b c d そうです f g h 私 j k VDIディレクティブ3210: 挿入ドリルによる深い掘削のガイダル値 。ベルリン、Beuth-Verlag、1996年。
- ↑ U. Heisel、R。Eisseler: 必死の掘削中のハイブリッド処理。振動の分離によるチップ長の影響 。 VDIは1987年、Düsseldorf2006を報告しています。
- ↑ J.ステッパン: 代替製造プロセスを通じて、L/D比500を大きくする穴のセンターコース削減 。 VDIは2142、Dortmund 2011を報告しています。
- ↑ a b D.ビアマン、F。ブライヒャー、U。ハイデル、F。クロック、H.-C。 Möhring、A。Shih: 深い穴の掘削 。の: CIRP ANNALS 。第67巻、2018年号2号 S. 673-694 。
- ↑ a b D.タムケ: 乾燥作業の可能性と限界、産業と大学の間の技術的な議論「現代の生産プロセスにおける掘削と製粉」 。 Dortmund 1997。
- ↑ P.ミュラー: 深い掘削のためのハイパフォーマンス会話ドリル 。 VDIは1897、Dortmund 2006を報告しています。
- ↑ T. Upmeier: 深い掘削のための革新的なプロセス設計 。 VDIは2142、Dortmund 2011を報告しています。
- ↑ VDIディレクティブ3209: 冷却潤滑剤の外部給餌による深い掘削(BTAおよび同様の方法) 。 Beuth-Verlag、ベルリン1999。
- ↑ U.ウェーバー: 深い掘削プロセスの測定への貢献 。 Gräbnerを印刷、1978年Altendorf。
- ↑ a b O.ウェバー: BTAディープドリルにおける掘削の深い依存プロセスダイナミクスに関する研究 。 Vulkan Verlag、Essen 2006。
- ↑ a b c d H.フット:2014年4月1日現在、www.iedbohren.info。
- ↑ W.König、F。Klocke: 製造プロセス2-研削、磨き、発売 。 Springer Verlag、Heidelberg 2005、ISBN 3-540-23496-9。
- ↑ a b D.ベアマン: BTAディープドリルにおける表面パラメーターの専門の実験室の決定へのスクリプト 。 Dortmund 2010、Spreading Spreading Manufacturing研究所。
- ↑ a b F. Klocke、W。König: 製造プロセス1-ターニング、フライス、掘削、掘削。 8.エディション。 Springer-Verlag、Heidelberg 2008、pp。163–176。
- ↑ T. Bruchhaus: BTAディープドリルツールを最適化するためのトライボロジー研究 。 Vulkan Verlag、Essen 2001。
- ↑ E. Plauksch、S。Holsten、M。Linß、F。Tikal: Szerpantechnik:プロセス、ツール、テクノロジー。 12.エディション。 Vieweg+Teubner-Verlag、2008年。
- ↑ ボテック: 精密掘削技術GmbH 。ホイール、ドイツ。
- ↑ M. Eckhardt: 状況、コース、穴の同軸の実際の決定 。の: テクニカ 。 いいえ。 十 、1977年、 S. 678–682 。
- ↑ E.ディングリンガー: ディープホール掘削ツールの新しい経験 。の: ワークショップテクノロジーと機械工学 。 バンド 45 、 いいえ。 8 、1955年、 S. 361–367 。
- ↑ B.Stürenburg: チップの形成を最適化し、Al-Alloysの掘削のためのワークピースのチップエントリを最小化する 。論文。カイザースラウターの工科大学、2009年。
- ↑ H. O.Stürenberg: 深い掘削の中央コースのために。パート1 。の: 金属処理用のTZ 。 バンド 77 、 いいえ。 6 、1983年、 S. 34–37 。
- ↑ F.ブライヒャー、A。シュタイニンガー: ボアのボアを減らすための深い掘削プロセスの積極的な影響。 。の: VDI会議の精度と深い掘削 。 2017年。
- ↑ C. Deng、J。Chin: タグチ法によって分析された深い穴掘削の穴の丸み 。の: Int J Adv Manuf Technol 。 バンド 25 、 いいえ。 5-6 、2005年、 S. 420–426 。
- ↑ K. D.エンダール: クーラント脈動によるフリンジディープドリルの際の中央コースコースの削減 。論文(= シュトゥットガルト大学の工作機械研究所からの報告 。 バンド 6 )。 1994年。
- ↑ U.ハイデル、T。シュテール、R。アイシセラー、P。ヤコブ: より生産的なより高い – ハイハード鋼のクッションとより長いダウンタイムのおかげでプロセスの安定性が高い 。の: ワークショップと運用 。 いいえ。 12番目 、 2013、 S. 68–71 。
- ↑ T. Ishida, S. Kogure, Y. Miyake, Y. Takeuchi: パイプ内可動メカニズムを使用した電気放電加工による長い湾曲した穴の作成 。の: Journal of Materials Processing Technology 。 バンド 149 、 いいえ。 1-3 、2004、 S. 157–164 。
- ↑ L. C.ケテット: ガンドリリングハンドブック 。 4. auflage。キャンベルバイキングプレス、ノースヘブン2010。
- ↑ B.グリナー: BTA手順に従って油圧シリンダーの生産 。の: 機械の世界 。 バンド 4 、1962年。
- ↑ J. Jung、J。Ni: ガンドリリングプロセスにおける冷却剤圧と体積流量の予測 。の: J.マンフ。 SCI。一。 バンド 125 、 いいえ。 4 、2003年、 S. 696–702 。
- ↑ F. Pfleghar: インレットディープドリルツールを使用するときのボア品質の改善 。論文。シュトゥットガルト大学、1976年。
Recent Comments