Stranggießen – ウィキペディア

注ぐ は、鉄と非鉄の合金で作られた半積み上げの生産のための継続的な鋳造プロセスです。鋳造するとき、金属は冷えた底なしのコークスと冷凍ボウルを通して注がれ、主にまだ液体のコアが横になっています。ストランドはスルースターの後に共有されます。
注ぐ と混同しないでください ストランドプレス 、たとえばアルミニウムからの完全なプロファイルと中空チャンバープロファイルで、プラスチック (押し出しを参照) セラミックが作成されます。
coconryの配置によれば、水平鎖と垂直鎖と垂直方向の鎖が区別されます。水平鎖鋳造は主にです [初め] 非アイアン金属に使用されます。湾曲したクーチルを備えた垂直鎖鋳造植物は、水平にそれを引き離すことができるように、ベントの半ステワードを注ぎます。その後、分離する前に、水平に到達した後、半頑丈なものをセットアップする必要があります。垂直ココノールを使用すると、キャスティングピースの長さがシステムの高さによって制限されるか、鎖を滑らかなコアで曲げ、水平に到達した後にすぐに指示する必要があります。
非鉄の金属の場合の垂直注入のために、開いた水冷銅コイルも底部に使用され、カラークールとも呼ばれます。液体金属には、散水速度で継続的に継続的にディストリビューターシステムが継続的に供給されます。最も単純な形では、溶けた炉とタンディッシュとも呼ばれるクーシルの間に注がれています。ストランドボウルは、最初はまだ液体コアを囲むコーラ内に形成されます。コーラから逃げる鎖は、さらなる冷却を好む骨盤に下げられ、常に水を吹き付けます。不連続な手順の場合、この冷却プールの深さは、スティック、バー、またはロンダーの長さを制限します。
ストランド鋳造システムは、1つ、2つ、またはマルチプレイスで構築されています。交差セクションが小さいほど、上流の集合体の容量を満たすにはより多くの鎖が必要です。対照的に、特に丸いバー(RondenまたはPress Boltsとも呼ばれる)をキャストする場合、Cocillaシステムが使用されているため、120〜150 mmの範囲の直径の最大32レースを同時に注ぐことができます。
鋼、銅合金、アルミニウムが加工されているかどうかにかかわらず、鎖鋳造の技術はほとんど違いがありません。主な違いは、純粋または合金アルミニウムを含む約700°Cから鋼の1600°Cを超える温度です。 19世紀半ばに継続的にキャストしようとする試み。決定的な進歩は1930年から行われました(軽量および重金属のためのJunghans-Rossiプロセス)。
コシラ鋳造の個別に形成された鋳造とは対照的に、ストランドキャストは、連続プロセスから根本的なセミコントです。このように動作するシステムの場合、それらの高さは、それぞれのストランド鋳造製品の最大長を決定します。継続的な作業とは、無限の鎖に水をまくことを意味します。これは、ストランドの一部が十分に凍結されるとすぐに、のこぎり(「飛ぶ鋸」)で分割するか、鎖が弓にリダイレクトされ、システムを水平鎖として残します。この手法は、とりわけ、フォームファンディー用のストランド鋳造グラインダーを生産するとき、または銅材料を極材料またはパイプに処理するときに使用されます。また、銅合金で作られた溝の鋳造で [2] 水平方向と垂直の両方でキャストされます。
ストランド鋳造製品は、最終製品によってさらに処理プロセスを受ける必要があるため、半分頑丈と呼ばれます。ほとんどのローラー、プレス、および深い描画が使用され、室内または周囲温度での以前の時間のかかるアウトソーシング、または上流または下流の熱処理(開始およびアウトソーシング)と組み合わされます。
特別な技術 [ 編集 | ソーステキストを編集します ]

ストランド鋳造システムは構成されています [3]
- スチール製の鋳造パンを挿入するためのpfannendrreh turm、
- 溶融物をコシラに導くディストリビューター、溶融物を導く
- 溶融物(一次冷却エリア)のあるcoconry、
- ダイビングチューブとシャドウチューブ
- 液体鋼を調整するためのスレート
- コシラ振動と保持デバイス、
- 二次冷却を伴うストランドガイドシステム(鋳造アーチ)、
- ドリフトと方向の工場、
- 中止ロール、
- 横部分システム(燃焼切断システム、はさみ)、
- マーカー(署名)と
- 風邪。
溶融物は通常、溶けたユニットから水を越えてストランド鋳造システムまでSO -Caltedフェリーで輸送され、Pfannendrreehmで使用されます。メルトは、スライドで閉じられているグラウンドアウトレット(出力)を介してディストリビューターに流れ込みます。液体鋼が空気酸素と反応しないように、液体鋼はシャドウチューブに導かれるか、ウォーターパウダーで覆われています。ディストリビューターは最初に緩衝容器の機能を満たし、パンの交換中にストランド鋳造プロセスの中断がないようにします。さらに、マルチストランドシステムのディストリビューターには、液体鋼を個々のストランドに分配する機能があります。メルトは、スラグ層(主にライスシェルアッシュ)でディストリビューターで覆われています。
メルトは、ディストリビューターから、またはダイビングチューブ(散水チューブとも呼ばれる)からコーラに自由に走ります。流れは、プラグまたはスライドを備えたコシラの散水鏡に応じて制御されます。 Tonerde(al 2 o 3 )避けるために、アルゴンで部分的にすすいで溶融物をゆっくりと電磁装置に減速または攪拌して、液体鋼の流れに影響を与える可能性があります。クーシルの散水鏡はスラグで覆われています。これにより、溶融物の再酸化が防止され、2階に結合し、冷凍ボウルとクーシルの間の潤滑剤として機能します。スラグを形成するために、水粉末は散水鏡に継続的に塗布されます。鋳造中に、コシラが動き回り、コシラ(銅板やニッケルプレートなど)の冷却された壁の鋼鉄を防ぎ、輸送プロセスをサポートします。コークスを離れると、鎖には厚さ数センチの冷凍ボウルがありますが、交差セクションの大部分はまだ液体です。 coconryの下では、いわゆるキャスティングシート(地区ゾーン半径10 m)の鎖は、空気/水検査(セカンダリ)によって外側から冷却されます。また、ローリングによってサポートされており、ストランドに作用する虫圧が原因で発生する膨張の程度を減らします。これらのストランドガイダンスの役割は、最高のストレスにさらされているが、鎖表面への影響のため、鎖鋳造システムの中心的な成分の1つです。このため、役割には、以前に溶接されていた腐食と耐摩耗性の層が提供されます。今日、これらの役割は、スピンキャスティングプロセスで「キャスト」としてますます製造されています。
鋼は、アルミニウムや銅などの他の金属と比較して比較的低い熱伝導率を持っています。これにより、キャスティングミラーから溶融物の完全な凍結まで最大20 mの大きな鎖長が生じます(そのため、「冶金の長さ」と呼ばれます)。ストランドは、スルーテンダーの後にのみ個々の橋に切り込むことができます。コシラを離れた後のストランドが垂直に継続されるシステムを使用するため、高さが大きく、めったに使用されません。ほとんどのシステムでは、鎖は約7〜15 mの半径(鎖の厚さによって異なります)で、水平角に到達したときに到達したときに曲げとガイドラインで再びまっすぐになります。クーシルはまっすぐに実行するか、曲がって実行できます。まっすぐなココノールでは、ストランドはコチラを垂直に降りて、その後のローラーガイドによってのみ曲がっています。どちらの概念にも特定の利点と欠点があります。これは、一方では鎖の曲げがリスクを引き起こし、一方で長い垂直液ルートがスラグに上昇する可能性があるため、鋼の純度に長い垂直液ルートが利点を提供するという事実に起因します。剛性の後、ストランドは排出ローラーコースの長さに切断されます。
ピアスの場合、下または上部から上部を閉じる、スタート – アップ(コールドハーベスト)がコシラに挿入されます。充填された鋼は開始ラインに固化し、それで引き下げられます。冶金の長さに達した後、開始線と鋳造鎖は互いに分離されます(不明)。
最終製品に応じたプロセスタイプ [ 編集 | ソーステキストを編集します ]

注ぎの場合、鋳造されるストランドの形式に依存するいくつかの方法を区別します。
- 丸いまたはほぼ正方形の断面(スティック)またはプロファイル型の断面さえ、スティックとプレブロッキングキャストに流されます。ポール、ワイヤー、プロファイルを製造するのに役立ちます。
- ブリッジは、BrammentRangguss、つまり、板金生産のために大きな幅(最大2600 mm)と小さな厚(最大600 mm)の長方形の鎖で生成されます。ブリッジングに関しては、次の間の区別が行われます。
- brammentrangguss全般(厚さ100 mmから600 mm)
- プレフォームキャストまたは(厚さ70〜300 mm)
- Dünbramtキャスト(厚さ40〜100 mm)
- 費用(厚さ15〜50 mm [4] ))
- バンドキャスト(厚さ数mm)。
後者の2つの方法では、投資技術とエネルギーバランスの分野でかなりの節約が可能です。形成プロセスのさらなる削減は、薄いバンドキャストによって達成されます(そこを参照)。
外科医 [ 編集 | ソーステキストを編集します ]
開口部の注ぎは、厚さ約50 mmの薄い脳で生成され、暖かいローリングミルの生産通りに直接穴を開けることができます。キャスティングマシンとローリングユニットの間には補償炉のみが必要です。この手順では、多くの鋼品質を低コストで処理できます。短所は、靭帯の柔軟性と表面の質が低いことです。
バンドキャスティング [ 編集 | ソーステキストを編集します ]
バンドキャスティングは連続的な鋳造プロセスであり、金属製のバンドが作られます。これは、形を形作られていないか、いくつかのステッチでのみ変換されません(ローリングフレームを通過)。このプロセスは、主に非鉄の金属に使用されます。
Stahlからの2ロールバンドのキャスティングは、19世紀にヘンリーベッセマーによって特許を取得しました。しかし、彼はそれを市場の成熟度に入れることができませんでした。 1990年以降、ステンレス鋼や電気鋼に産業的に使用されています。ここでは、鋼は2つの回転水ローラーの間で凍結し、厚さ6 mmの最大でバンドとして完全に凍結されています [5] 、削除されました。鋳造ローラーの速度は、完全な固化(水温やローラー速度が高すぎる)がない場合、ブレークスルーが発生するため、キャスティング温度に合わせて正確に調整する必要があります。ただし、メルトが早すぎて凝視されている場合、ローラーの力は大きすぎてプロセスを麻痺させることさえできます(水温やローラー速度が低すぎます)。
ローリングフレームワークは通常、システムに配置されます。この枠は、1つのローリングステッチ、1 mmのバンド厚さ(同時に可能な最小結果)の後に(散水厚が少ない)。丸められた薄いバンドは水をまき、ローラーに包まれているため、「コイル」が呼ばれます。
この手順は、低い投資のニーズの利点と、より少ないゆるい生産の可能性を提供します。さらに、橋の露出に必要な回復はもはや必要ありません。コスト要因の時間とエネルギーにさらに節約があります。
Hilmar R.Müllerは、非鉄金属のストランド鋳造プロセスのほぼ完全な概要を提供します。 n-metalsのストラングキャスト – 概要 。の: ドレスデンでのマテリアルウィーク2015 。 n-metalsのシンポジウム18-Stranggießen、doi: 10.13140/rg.2.1.1251.3762/1 。
(2015)。 (非鉄金属の連続鋳造 - 概要)。
特別な技術 [ 編集 | ソーステキストを編集します ]
また、上の名前で分類されるアルミニウムのストランド鋳造は、他の人の場合のように、不連続または継続的なプロセスとして完了することができます。前者の場合、バーまたはロンドはシステムによって指定された長さで作られています。他のケースでは、専門家の表現によると、空飛ぶ鋸で特定の長さに到達した後のキャストストランドは、これは鋳造プロセスが続くときに分割されます。このテクノロジーは、半連続した真の連続性を上記の無限の鎖を提供するものとして説明することもできます。
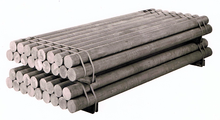
このような投資関連の区別に関係なく、液体金属はダガージュを介してアルミニウムにも追加されます。散水チャネルでは、キャスティング速度に応じて、重要な添加物を合金に追加できます。ほとんどの場合、それは艦隊(穀物の敵)の影響のためのチタンとホウ素を含む偏向です。
一次冷却で急速に保存された水冷クーチルのストロークは、さらなる冷却と統合のために冷却プール(二次冷却)に控除されます。コシラのサブセットと流入は毎回行われます。 5〜15 cm/minの鋳造または低速度は、小屋合金によって決定されます。
鋳造構造には、金属融解の異なる凝固速度が常に見えます。たとえば、水冷によって引き起こされる固化により、水冷による相排泄物はありません。つまり、スペクトル分析スペクトル分光造影の組成に通常違いはありません。ただし、鎖鋳造中の急速な熱降下は、凝固構造内の緊張からの電圧を防ぎます。コールドアウトレイまたは温かい治療(ソリューショングロー)は、保持しているときにひび割れにつながる可能性のある緊張を排除します。したがって、鋳造皮膚の汗をかいているセイラーのような汗は、治療されないため、さらに処理する前に鋳造皮膚が粉砕されます。空気が熱放散を妨げるため、頑固な金属とcoconious壁の間の合金依存の収縮ギャップを可能な限り小さく保つように注意する場合、鋳造 – 技術的エラーは制限される可能性があります。 [6] シュリンクギャップよりもはるかに大きな問題は、アルミニウムとその合金を注ぐときの水素吸収と酸化物の形成に関する液体金属の感度であり、それぞれが溶融物の特別な処理を必要とします。
Stranggussでの融解治療 [ 編集 | ソーステキストを編集します ]
水素吸収、回避、距離の問題 [ 編集 | ソーステキストを編集します ]
主要な小屋に従属している鋳造所に鋳造された鋳造所に鋳造されている場合、それは、純粋なアルミニウムであろうと、溶けた場合、またはすでに基づいて既に合金化されている金属の場合にのみ、事前に配達されます。ブレンダーまたは温暖化オーブンで行われる治療は、主に、汚染された電気分解の溶融物の溶融物を解放することを目的としており、これはナトリウムとカルシウムへの給与の大幅な減少を意味します。常に与えられた水素含有量の除去は、最新の可能な場所で実行されます。世紀の変わり目の前に、塩素ガスまたは塩素放射添加剤を使用して塩素酸塩が好まれ、2つの干渉要素を塩化物にすばやく移し、スラグに上昇させました。同時に、過剰な塩化アルミニウムは、全体的な温度の下で溶けを残すため、有用なすすぎ効果をもたらしました。環境保護の理由により、塩素の使用は1980年からますます減少し、アルゴンまたはフロオンは低塩素で使用されました。処理チャンバーと呼ばれるSNIFボックスの発明は、分布システムに直接スイッチされたため、無駄にする前に最後の場所でより細かい投与量と除去を可能にするため、湿った周囲の空気から再開する可能性が制限されます。最先端は、ワイヤーがさらに割り当てられている場合、必要な穀物の女性を配置することでもあります。酸化物の除去は、治療の過程で洗浄されていない限り、ろ過の責任です(そこに参照)。
溶けたスクラップはしばしば腐食しているため、つまり水酸化物層で溶けたり、溶けたりするため、特に水素を除去する場合、特に水素を除去する場合は、スクラップから鎖鋳造材料を生成することができるリサイクル会社がもう少し実行する必要があります。また、リサイクル材料は部分的にフォームファウンドリーで作られており、多数の望ましくない要素を含めることができるため、干渉要素に注意を払う方が強くなります。それらのすべてが必要な、または削除できるわけではありません。マグネシウムまたは銅を使用すると、材料に安全な材料を提供できます。シリコンが豊富なメルトは、ALSI鋳造合金の生産により適しています。 [7]
酸化物の形成、回避、距離の問題 [ 編集 | ソーステキストを編集します ]
アルミニウム、特にマグネシウムの酸化傾向がアルミニウムを溶かす場合、阻害測定を使用して酸化を制限する必要があります(融解処理)。キャストに注がれた溶融酸化物では、ほとんどがカッターの形でのガンマ酸化物が常に鋳造エラーにつながります。
鋳造技術の場合の酸化に対する保護に注意してください。コンバージョンプロセスを通過するストランドの場合、鋳造ビームだけでなく、配信システムでも実行できます。ろ過は、最新技術に従って優れたセキュリティを提供します。
溶融 [ 編集 | ソーステキストを編集します ]
フォームストラップ(半製品)または鋳造フォームの場合でも、特別な品質要件が配置されているアルミニウム製品の生産については、酸化物包含物を避ける必要があります。酸化を回避できない限り、すすぎによって融解をきれいにする必要があります。過去には、これは溶融物の処理、すなわち、ボトルから、またはその場での気体塩素の通過を抑制することによって達成されました。今日の視点では、アルミニウム融解の塩素化には異なる欠点があります。とりわけ、溶融物のマグネシウム含有量が減少し、特に環境保護の問題が発生します。これは、形成されているつかの間の塩化アルミニウムが溶融温度で部分的に環境に入ることができるためです。塩素への対処は、職場の衛生にとっても望ましくありません。したがって、今日、低塩素部品の不活性ガスまたは混合物が使用されています。 [8] 分解と同時に、水素含有量を減らして洗い流し、水素で粗い酸化物を除去します。微細な酸化物も検出する追加のろ過によって補充できます。
2つのろ過方法が最先端です。ポルノセラミックフィルターのいずれか、または通常はガソリンコークスで作られた溶融物を流れるフィルターベッドのいずれかです。両方の方法は、溶融物が発生する前に酸化物を傍受するのに適しています。
陶磁器に指定された性質として指定された冶金使用のためのフィルター – 電気工学で使用される同じ名前の周波数フィルターと混同されない – は、円形と正方形の両方であり、タスクに応じてcm²あたりの一定の孔があります。ストランド鋳造システムの配電システムに可能な限り近いため、交換する前に一定量の金属の流れが可能になります(フィルターが一度)。
アルゴンまたは乾燥窒素からのガス制御は、このタイプのスループットろ過に設置できます。治療後の含有量は、0.08 mL/100 gアルミニウムでなければなりません。
観察されるろ過の利点は、酸化除去に関連する水素の再開の減少です。酸化物を含む溶融物では、湿った周囲の空気からの水素を使用して、溶解度の制限をはるかに上回る溶解制限をはるかに上回る溶融物と水素を使用できます。適切な塩混合物でバスルームの表面を保護することができる限り、空気よりも重い保護ガスで。
- ↑ Schmelzen/Gießen -Bgh Steinstahlwerke Gmbh。 2021年9月16日に取得 。
- ↑ すべての銅材料のほぼ90%が、鎖鋳造プロセスで半描画された製品に継続的または不連続に処理されています。 American、Publisher Schiele&Schön、Berlin 1986、ISBN 3-7949-0444-3から翻訳された銅合金からの鋳造、Brunhuberを参照してください。
- ↑ 1948年にスチュリアのブライテンフェルドステンレス鋼工場で、世界初の大規模な鎖鋳造システムが稼働しました。
- ↑ http://kerschgens.stahl-xikon.de/index.php/stahlollexon/56-V/2802-vorbandgie%C3%9fen.html
- ↑ https://www.hindawi.com/archive 2016/1038950/
- ↑ テクニカルノート:シュリンクギャップを削減するために、クーシルで可能な限り低い金属レベルでの水やりなど、時間の経過とともに多くの措置が提案されています。別のオプションは、円錐形または悲しみのあるcocilsの使用を提供します。成長したココメは、cocon的な壁と液体金属の間のエアポケットによる熱除去の遅延を引き起こします。そのため、金属がコシラのコシラの金属が立っている場合、金属は冷却表面に長く依存しますが、収縮もさらに下に移動し、収縮ギャップは短くなります。前世紀の前世紀の前世紀の後半には、当時のAlususseによってすでに実用的であり、シュリンクギャップの問題を扱っていた磁場の接触型ストランドキャストは、すでに実用的でした。
- ↑ テクニカルノート:表面上の水蒸気圧が大きく、溶融の温度が高いほど、溶融物のバランスとして調整される水素含有量が高くなります。アルミニウム中の水素の平衡に対する温度の影響を図1に示します。高温溶融物の水素レベルの可能性は、図1にhatch化しています。このような含有量を減らす必要性は、固化後のアルミニウムの水素溶解度が液体温度での溶解度の10未満に低下し、結果として生じる過剰は、たとえば、砂の鋳造で遅いほど、キャストの爆発的な空洞よりもはっきりと示されることです。非常に迅速な凝固が発生した場合、金属形式の形式で鋳造された形式の場合に示されているように、粗い爆破排泄の危険は減少し、細かい気孔率または細かい気孔率が低下します。もともと溶融物に溶解した水素には、急速に恐ろしい構造から溶けてしまうのに十分な時間がありません。つまり、より高い水素含有量は、バランスの状態に可溶性よりも密度サンプルを使用するなど、冷凍キャストで一般的に決定されます。
- ↑ これに基づいて動作するデバイスは次のとおりです スニッフ これにより、「スループットプロセス」で洗浄を溶かすことができます。
Recent Comments