マシンエンジン – ウィキペディア
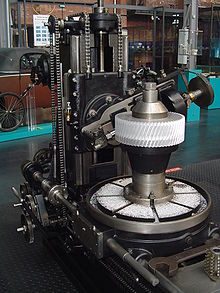

工作機械 ツールを使用したワークピースを生産するためのマシンであり、その動きはマシンによって指定されています。 [初め] 最も重要な代表者には、撮影および製粉機、侵食マシン、機械的なプレス、マシンハンマーが含まれます。
彼らの部門には、互いに関連する標準DIN 8580 FF(手順)とDIN 69 651パート1(金属処理)があります。工作機械には、ツール、ツール、デバイス、測定機器、テスト補助具とともに含まれます。それらの多様性のため、それらはさまざまな基準に従って分割されます。根本的な製造プロセスに従って、変換と分離(基本的に:分割、欠け、病気)、およびマシンの提出。従来のマシン、マシン、CNCマシン、加工センター、柔軟な製造セル、柔軟な製造システム、柔軟なトランスファーストリート、従来のトランスファーストリートで自動化した後。
最新の工作機械はほとんどモジュール式です。最も重要なアセンブリには、フレーム、ドライブ、ガイド付きツアー、コントロールが含まれます。他のアセンブリとして、基礎、ツールメモリとチェンジャー、ツール記録、ワークピースチェンジャー、測定システム、供給および処分施設があります。
石器時代には工作機械の先駆者がいたかもしれませんが、現代の意味での最初の工作機械は、イギリスの産業革命の始まりにのみ作成され、すべての工業化された国で非常に迅速に広がりました。当初、いくつかの機械は単一の蒸気エンジンで駆動されていました。1900年頃から、各マシンは独自の電気駆動を受けました。 20世紀半ば以来、そのさらなる発展は、主に自動化と柔軟性によって形作られてきました。
工作機械にはいくつかの定義があります。ただし、機械に属するマシンが多かれ少なかれ粗い手がかりのみを提供します。とりわけ、原始的または頻繁なマシンは部分的にしか追加されていません。
Otto Kienzleによると定義 [ 編集 | ソーステキストを編集します ]
工作機械で頻繁に使用される定義は、Engineer and Universityの教師であるOtto Kienzleに由来しており、DIN 8580によると製造プロセスの部門も登場します。 1969年に彼の死後、最先端をより良くマッピングするために拡大されました。
- 工作機械は、相互の特定のガイダンスの下で、ワークピースのツールを効果にもたらすワークマシンです。 (Kienzle) 製造プロセスに関する情報とワークの取り扱いと記録、処理、および取り戻しを引き継ぎます。 (拡大) [2]
このタイトな定義は、さまざまな同様のマシンと比較して工作機械を区切ります。 [3]
- 指定を通して ワークマシン 発電機、エンジン、ギアなどのエネルギーの「生産」または変換を提供するすべてのパワーマシンが除外されている場合。
- 工作機械は、製造と処理に役立ちます ワークピース 。定義のこの部分は、フロー製品を生産するエンジニアリングマシンを処理するための境界として機能し、本の包帯やパン切断機などの他の多くの種類のマシンと比較して機能します。
- 工作機械を使用します ツール 。これらは、ドリル、粉砕ツール、ノミ、水、レーザー、電子光線、またはバーナーの炎などです。可能なすべての製造プロセスを適用します。
- ワークとツールは必要です 工作機械によって相互に決定されます なる。ツールとワークピースの位置、およびその動きは、人間ではなく機械によって決定されます。これは、ドリルドライバー、刺し傷、角度グラインダー(「フレックス」)などのモーター駆動型の、しかし手渡されたツールからの境界として機能します。
DIN 69 651による定義 [ 編集 | ソーステキストを編集します ]
din 69 651では、工作機械は ワークピースとツールの間の相対的な動きにより、ワークピースの特定の形状またはワークピースの指定された形状の変更を生成する機械化された、多かれ少なかれ自動化された製造デバイス。 [4]
初期の先駆者 [ 編集 | ソーステキストを編集します ]
石器時代の石の軸にきちんと掘削された穴があるため、ウィルヘルミニア時代以来、6000年前に非常に呼ばれるフィデル掘削機があった可能性があると推測されており、アーチの腱がフレームに巻き付けられているドリルに巻き付けられています。弓をやり取りすることにより、ドリルを交互の回転に置くことができます。このようなデバイスは、すでに工作機械のすべての機能を満たしています。ただし、考古学的な証拠は欠落しているため、これらのレプリカ掘削機が19世紀に一般的な工作機械でモデル化される可能性があります。
最初のスイベルベンチと、粉砕機と掘削機が古代に登場しました。これは、ゲーペルの水力発電や動物によって駆動されました。ただし、ツールは引き続き手作業で管理されていました。ルネッサンスでは、レオナルド・ダ・ヴィンチがさまざまなワークピースを生産するための機械を開発しました。その中には、掘削機、シェードのファイリング、糸の切断またはシリンダーループのためのマシンがありました。 1771年、最初のコピーライターが開発され、そのツールは、定義されたパスに沿ってマシン自体によってすでに導かれていました。 [5]
産業革命の間 [ 編集 | ソーステキストを編集します ]

工作機械は、強力な蒸気エンジンの生産の前提条件でした。その結果、蒸気エンジンは、新しく作成された工場で多数の工作機械のドライブとして機能しました。大気ピストン蒸気エンジンは、1712年にトーマスニューコメンによって発明されました。ただし、直径約1メートル、長さ2メートルの必要なシリンダーを構築すると、当時は機械の限界に達しました。2センチメートルの寸法偏差は良い結果と考えられていました。 1775年、ジョン・ウィルキンソンは、数ミリメートルの偏差を確実に観察した水平訓練をなんとか構築することができました。シリンダーを鉄で退屈させることにより、蒸気エンジンの建設を建設に可能にしました。これは、ジェームズワットによって考案されました。
最初は繊維産業でも、その後、他の多くの地域でも、繊維産業の機械の需要が継続しているため、蒸気エンジンは急速に広がりました。関連する技術的および社会的混乱は、最初の産業革命と呼ばれます。高精度の需要は、通常の手動作業ではなく、工作機械を使用するために重要でした。中央の蒸気エンジンから機械ホールを通過するトランスミッション波。そこから、エネルギーは革のストラップを介して個々の機械に転送されました。産業革命の過程で、生産技術の多くの分野でさらなる進展があり、それが互いに施肥し、それらを前進させました。木炭の代わりに硬質炭を使用することにより、より正確な工作機械のツールとフレームにすぐに使用される鋳鉄製の生産が可能になりました。材料としての鉄の使用の増加により、工作機械の需要が増加しました。 [6]
重要なマシンタイプの開発 [ 編集 | ソーステキストを編集します ]

工業生産にとって特に重要であることが証明されています 旋盤 。イギリスのヘンリー・モードレイによって大幅に改善されました。彼は、クランクを通過できるツールホルダーで最初の旋盤を構築しました(飼料とのサポート)。その前に、ツールはまだ手作業で管理されていたため、作業結果は労働者のスキルと経験に強く依存していました。 Maudslayの開発により、マシンはより正確になり、仕事のパフォーマンスが高く、使用が激しくなく、動作するために必要なトレーニングが少なくなりました。何よりも、後者は新しい技術の急速な拡散にとって重要でした。なぜなら、経験豊富な旋盤は非常にまれであり、イギリスの移民が禁止されたからです。 Maudslayは、ネジと糸の生産のための旋盤も発明しました。その前に、それらは手で作られていたため、すべてのスレッドが個別になりました。マシンの精度が向上したため、初めてネジを製造することができ、それらが交換可能であるため、ネジを正確に製造することができました。
さらなる改善は、ジョセフ・ホイットワースだけでなく、2人の学生であるモードスレイズリチャード・ロバーツとジェームズ・フォックスからもたらされます。より速い処理のために、いくつかのツールを備えたマシンも開発されていました。 1845年、コネチカット州のアメリカのジョン・フィッチは、いくつかのツールがリボルバーにあるため、迅速に変更できる最初の回転機械を建設しました。 18世紀の終わりに向かって、最初の機械的に制御されたロータリーマシンがアメリカで建設されました。
1800年から1840年の間 カラムおよびスタンド掘削機 ウィットワースとウィリアムフェアベアンによって開発されました。スパイラルドリルは、1867年のパリ世界展示会で初めて展示されました。ただし、価格が高いため、尖ったドリルに勝つことができるまで高価格にもかかわらず、1890年までかかりました。
の最初の構造 ホーベルマシン まだMaudslayから来て、彼の学生ロバーツは機械式フィードを備えた最初のバリアントを構築しました。最初のアメリカンプレーナーは、1833年にゲイシルバー&Coから提供されました。ドイツの工作機械の建物の創設者の一人であるヨハン・フォン・ジマーマン(彼は大陸で最初の工作機械工場を建設しました)は、1862年のロンドンワールド展で彼のプレーニングマシンに対して賞を受賞しました。

最初のフライスツールには、まだ最も古い保存されているジャックバンカンソンがいると言われています 製粉機 コネチカット州のアメリカのエリ・ホイットニーから来ています。コネチカットは武器生産でそれらを使用しました。 1860年の最初の自動ユニバーサルミリングマシンは、アメリカのジョセフブラウンから来ています。1900年頃まで、粉砕機の機械も技術的に成熟していました。
特にモデルと武器の構築において、精度の請求が増加した結果、粉砕が重要になりました。最初 研削盤 Alfred Kruppは、1833年の金属処理に起因しています。 1853年、ヒラム・バーカーとフランシスは、蒸気機関車のバルブに必要な真鍮ボールを粉砕するためのマシンの特許を取得しました。 1855年、W。Muir&Co。は、マンチェスターでナイフとサウンド用のツール研削盤を構築しました。
1842年にイギリス人のジェームズ・ナスミスが蒸気駆動型を建設しました Schmiedehammer 。ハンマーベア(ツール)は、蒸気エンジンのピストンによって上げられ、ワークピースに落とされました。その結果、鍛冶屋はこれまで可能でした。 Alfred Kruppは、30トンのケース重量で巨大な蒸気ハンマーを構築し、最大2.5トンの鋳鉄製ブロックを処理できました。 1860年には、最初の油圧鍛造ハンマーがありました。 19世紀の終わりに、最初のシャフトスミスマシンが開発されました。
古典的な工作機械の開発と対応する製造プロセスは、1900年頃に本質的に終了しました。今日知られているほとんどすべてのタイプが存在していました。 [7]
影響 [ 編集 | ソーステキストを編集します ]
工作機械の開発は、社会的、組織的、技術的要件の影響を受けました。一方、機械の一定レベルの開発により、これらの影響が可能になりました。
プラグインニードル生産の有名な例を通じて、アダムスミスは、作業部品の生産プロセスによって生産性が大幅に向上する可能性があることを示しました。単一の未熟練労働者は、1日で数個のピンしか生産できません。作業がいくつかのハンドル(首謀者、ラッピング、抽出など)に分かれている場合、たとえば、5人の労働者が1日で数千のピンを生産できます。針などの個々のワークピースの場合、そのようなシリーズや大量生産が実現することができます。ただし、機械や武器などのマルチパート商品の生産には、個々の部品が交換可能であることを確認する必要がありました。この生産モードは、交換ビルと呼ばれ、とりわけ、わずか2年で10,000人を超えるマステッターを命じたエリ・ホイットニーによって実現されました。一方、工作機械はますます作られ、この精度は機械と武器の大量生産のみを可能にしました。
アメリカでは、19世紀に労働者が不足しており、特に資格がありました。したがって、可能な限り使いやすく、できるだけ早く作業した機械に、人間の仕事を可能な限り置き換えるよう努めていました。分業の方法は、1900年頃にフレデリック・ウィンスロー・テイラーによって科学的管理によって洗練されました。ヘンリーフォードは、テイラーの原則と組立ライン生産の導入を一貫して使用することにより、20世紀初頭に大量生産を完成させました。しかし、彼の生涯では、テイラーは別の発明で知られるようになりました:速い作業鋼。それにより、スパンの切断速度は約3倍に増加する可能性があります。ただし、既存のマシンのドライブとフレームは、このような高性能のために設計されていなかったため、生産性が高いためにリリースされた新しいマシンを構築する必要がありました。 [8]
2番目の産業革命 [ 編集 | ソーステキストを編集します ]
19世紀の終わりに向かって、機械は使用可能な蒸気タービンを生産するのに十分正確でした。世紀の変わり目に、最初の発電所が稼働し、電気エネルギーを生成しました。それらは最初は主に街路照明に使用されていました。第2の産業革命の過程で、燃焼および電気モーターの開発により、各マシンにはもはや近くに依存していない独自のドライブを装備することができました。この変更はいくつかのフェーズで行われました。伝送波の原則は、依然として工場で普及しています。大型のマシンがオフまたはオフになったとき、他のマシンは作業結果を悪化させるぎくしゃくした隆起に発生しました。したがって、最大のマシンには当初、独自のドライブが装備されており、残りを数年間送信について使用しました。
第2フェーズでは、中央の蒸気ボイラーが中央の電気モーターに置き換えられ、現在では伝送波が駆動されました。各フェーズでのみ、各マシンはドライブとして独自のエンジンを取得しました。個々のドライブへの移行は、高速作業鋼の開発によって好まれました。その潜在能力を活用できるようにするには、新しいマシンが必要でした。効率が悪かったトランスミッションを排除することにより、現在使用されているエネルギーが大幅に少なくなりました。その後、工作機械は各飼料車軸用に独自のエンジンを手に入れました。同時に、マシンは、最初に機械的制御のさらなる開発により、後に単純な電気制御または穿孔カードを使用してますます自動化されました。米国と日本はこの発展を主導していました。
科学研究 [ 編集 | ソーステキストを編集します ]
最初の技術および科学学校とアカデミーは、18世紀の間に設立されました。新しいタイプの最初の学校は、世紀の終わりに向かって開かれました:パリのポリテクニック学校。彼らのモデルによると、他の多くの学校はフランスやドイツ語を産む国で作成され、19世紀の間に技術大学にアップグレードされました。世紀の前半には、今日の製造技術の先駆者であるSOがコールした「機械技術」はまだ集中していました。ポリテクニックスクールのディレクターであり、後にハノーバーの大学のディレクターであるカール・カルマルシュは、「機械技術のシステム」に関する本を書き、研究と教育のツールのコレクションを作成しました。彼の後継者ヘルマン・フィッシャーは、1900年に工作機械に関する本を出版しました。そこでは、既存の機械を分類して説明しましたが、メインとマイナーの操作と重要性についても取り上げました。
生産技術の分野は、当時まだユニットでした。製造プロセスだけでなく、工作機械、鉱業や繊維機などの他の機械、会計(コストの決定)、工場の計画と運用が調査されました。 20世紀の初めに、工作機械のみを扱う最初の椅子が設立されました。 1900年頃、科学と実践の関係も変わりました。産業革命の間、機械工物をさらに改善したのは機知に富んだ起業家でした。科学はプロセスにのみ付随することができました。 1900年以来、生産のより良い理論的理解は、技術的な進歩の前提条件となっています。最初は、模範的なLudwig Loewe AGやTaylor自体など、一部の企業が研究について試しましたが、すぐに制限に達しました。現在まで、生産研究の大部分は、大学、研究機関、産業によって一緒に運営されてきました。専門学校や大学は、数十年の遅れてアメリカとイギリスでのみ設立され、いくつかありました。最も有名なのは、マサチューセッツ工科大学です。したがって、1900年頃、アングロサクソン諸国のよく訓練されたエンジニアの幅広い不足が顕著でした。 [9]
第三産業革命 [ 編集 | ソーステキストを編集します ]
1950年頃、数値制御がマサチューセッツ工科大学で開発され、コンピューターで複雑な幾何学を粉砕することが可能になりました。ただし、コントロールだけに必要なハードウェアは、従来の工作機械よりも高価でした。さらに、プログラミングには高い努力があったため、数値コントロールが最初に勝たないようにしました。 1970年代初頭のマイクロプロセッサの開発により、第3産業革命では、数値制御のコスト効果的なアプリケーションを可能にする独自のコンピューターを各マシンに装備することが可能になりました。 [十] プログラミングプロセスも簡素化されたため、新しいテクノロジーが迅速に広がりました。一方で、あなたの利点は、ほぼ望ましいジオメトリを作成する可能性であり、一方で高い柔軟性があります。別の製品タイプを生産するには、新しいプログラムをストレージにロードするだけでした。その結果、個々の部品と小シリーズの生産コストが大幅に削減されました。この効果は、いくつかの製造プロセスを組み合わせた最初の編集センター(BAZ)の開発によって強化されました。過去には、ワークピースを旋盤で最初に回してからさらに編集する必要がありました。両方の手順を習得する加工センターでは、2つのマシン間のスパンとワークピース輸送が排除されます。
最初の柔軟な製造システムにより、数値制御と材料の流れと取り扱い技術を開発することが可能になりました。彼らは、輸送機器(例:新しい産業ロボット)で接続されたいくつかの同じまたは異なるマシンを持っています。これにより、各ワークのシステムを介して個別の方法が可能になります。これからは、低コストで中型シリーズを製造することもできます。製造道路のロボット挿入により、これらは柔軟性を高めました。
20世紀の過去数十年で、ドイツと日本と米国は世界市場の指導者でした。 [11] [12番目] 2013年、中国は世界最大の生産者であり、世界中で買い手であり、その後に日本とドイツが続きました。 [13] 中国のNettoはまだ工作機械を輸入していますが、日本とドイツは重大な輸出余剰を持っています。他の重要なメーカーは、イタリア、台湾、韓国、米国、スイスです。生産の約3分の1とサプライヤーを含む自動車産業を備えた機械工学は、さらに3分の1のバイヤー産業であり、3分の1が3分の1です。
ツール、デバイス、測定エージェント、テストエージェントとともに、工作機械は機器の一部です。それらは多種多様な症状を持っているため、さまざまな基準に従って分割されています。最初のオプションはにあります シングルオフマシン 強く制限されたワークピーススペクトルのみが可能です(壁の製粉またはギア形状研削盤のローラーミリングマシンなど)、および ユニバーサルマシン さまざまなワークシェイプを作成することができます。それらは主に製造プロセスにちなんで命名されており、そのために主に回転機やフライス材などの設計されています(フライス装置で掘削することもできます)。さらに、それらは、軸の数(最大6)、メインスピンドル(水平または垂直)の位置、建設的な構造(クロスベッドのごみ)、運動学(平行またはシリアル)、達成可能な精度(標準、精密、精度、超高度のマシン、プロダクション(違い)に依存します(違います)。波)。 [14]
2つの最も一般的な分割オプションは、製造プロセスの主要グループの分割に類似しており、自動化の程度に応じています。
製造プロセスに従って分類 [ 編集 | ソーステキストを編集します ]
密接な視点によれば、機械工具の間でカウントされるのは、変換、スパン、および除去のマシンのみです。さらなる視点によれば、原始形成マシン(キャスティングマシンなど)、頻繁な、すべての分離機(分割、チッピング、ドロップオフ)も予想されます。
すべての工作機械の生産価値の約3分の2があるため、チップが最も重要です。回転機と粉砕機に加えて、掘削機、プレーニングマシン、チャンクエンジン、部屋、ソーイングマシン、研削盤、大した、帆船も含まれています(賞賛のため)。 [15]

フォーミングマシンは、製造プロセスに従って曲げ機、プレス、描画機(引っ張るため)、ローリングマシンにさらに分割できます。ただし、さまざまなツールのインストールを通じて、いくつかの製造プロセスを実装できます。したがって、根本的な機能原則に従って分割が証明されています。で エネルギー – バウンド形成マシン すべてのハブでは、同じ量のエネルギーがワークピースに影響を及ぼします。これは、Fallhammerと同様に、常に特定の高さからツールをドロップすることで実現できます。過圧およびカウンターストロークハンマー、およびスピンドルプレスもこのグループに属します。 結び付けられたフォーマルマシン ストロークごとに同じように置きます。これには、エキセントリックなプレス、クランクプレス、膝レバーが含まれます。パワーバウンドの人々は、特定の力に達するまでワークピースに基づいて行動します。これには、油圧プレスが含まれます。 [16]
分散マシンは、構造の構造物と非常によく似ており、衝撃はさみ、切断プレス、パンチングマシンに分かれています。それらは主にシートを処理するために使用されます。
除去された機械は、基礎となる方法に従って、侵食機、レーザー加工機、水ジェット切断機に分割されています。生産性が低いためにコストがかかるため、他のマシンが使用できない場合にのみ使用されます。これは、たとえば、非常に硬い、脆性、脆性、または温度に敏感な材料を備えた場合、または非常に小さな形の元素と同様に飼育の製造に当てはまります。 [17]
自動化の程度に応じた分類 [ 編集 | ソーステキストを編集します ]
一 従来の工作機械 エンジンとトランスミッションを介して、ハンドホイールを介して切断および給餌の動きを作成します。 a 自動 フィードの動きはすでにそれに反対しています。 CNCマシンは、手動でクランプされたワークピースで自動作業サイクルを実行します。ツールの変更は通常、自動的に実行されます。加工センター(BAZ)は、ワークピースの変更とツール制御システムも統合します。柔軟な製造セルは、ツールマガジン、より大きなワークストア、Zを備えたいくつかのマシンで構成されています。 T.統合測定デバイス。柔軟な製造システム(FFS)には、製造制御または生産計画システムを接続するクロスマシン自動ワークフローがあります。従来の移動道路の柔軟性は非常に低いです。製品範囲の小さな変更は、精巧な準備によってのみ行うことができます。 [18]
通常、工作機械はモジュラーアセンブリから組み立てられます。これにより、構造が容易になり、個々のコンポーネントの量が多いため、生産コストが削減されます。個々のアセンブリは、多くの場合、顧客の要件に従ってまとめられます。 [19] 最も重要です フレーム 、 ドライブ 、 操舵 そしてその ガイド それは、ツールに特定の動きのオプションを与え、他の人を防ぐだけです。他のアセンブリがあります 基礎 、 ツールメモリとチェンジャー 、 ツール録画 、 ワークチェンジャー 、 測定システム としても 購入および処分施設 。
フレーム [ 編集 | ソーステキストを編集します ]
マシンフレームは機械加工力を吸収し、すべてのアセンブリの位置を保証します。大部分は、工作機械の静的および動的な剛性を決定します。小規模なマシンの場合、フレームはテーブルとして設計されています。重い機械の場合、ベッドの設計は、オープン(スタンドまたはCの構造)または閉鎖(ポータル)構造で使用されます。
-
-
ポータル構造(プレーナー)
-
ベッドフレーム(旋盤)
典型的なのは、鋳鉄、鋼、光金属、ミネラル鋳造(ポリマーコンクリート)または繊維複合プラスチックで作られたバージョンです。 Ultra -Ecisionマシンを使用すると、Franite Frameコンポーネントを見つけることもできます。それまでの間、発生した光金属も使用されます。 [20] 少ない量では、溶接またはねじ込まれた構造が好まれ、より多くの量のストーブを鋳造します。
フレーム材料の重要な特性は、弾性モジュール、密度、熱膨張係数、熱伝導率、伸縮制限と材料減衰、フレームの振動に減衰されます。ミネラル鋳造は、金属材料と比較して低密度と非常に高い減衰によって特徴付けられます。回復力が低いため、フレームは非常に大きくなければなりません。鋳鉄は、金属材料の良好な減衰によって特徴付けられているため、特に頻繁に使用される理由です。 [21] [22]
スタール | 鋳鉄 Ball Graphitit |
鋳鉄 ラメレングラフィット |
ミネラル | アルミニウム | |
---|---|---|---|---|---|
弾性モジュール[10 5 n/mm²] | 2.1 | 1.6 … 1.85 | 0.8 … 1.4 | 0.4 | 0.67 … 0.76 |
比重[n/dm 3 ] | 78.5 | 74 | 72 | 23 | |
熱膨張係数[10 -6 /k] | 11.1 | 9.5 | 9 | 10 … 20 | 21 … 24 |
比熱容量[J/(g・k)] | 0.45 | 0.63 | 0.46 | 0.9 … 1.1 | 0.88 … 0.92 |
熱伝導率[w/(m・k)] | 14 … 52 | 29 | 54 | 1.5 | 117 … 211 |
Dirror Benzees [n / mm] | 400 … 1300 | 400 … 700 | 100 … 300 | 10 … 18 | |
材料減衰[寸法なし] | 0.0023 | 0.0045 | 0.02 |
財団 [ 編集 | ソーステキストを編集します ]
特別な基盤は、大型のマシンにとって特に重要であり、通常、マシンの総質量の70〜90%の地面に注がれ、総質量の70〜90%のマシンの総質量があります。その慣性が高い全体的な剛性を保証し、静かなマシンの実行を通じて必要な精度を可能にするためです。特に、重度のワークピースの場合や高労働者の場合、またはショック様ストレスの場合、特にマシンファンデーションの対応する大規模な解釈は重要になります。そうしないと、マシンの部分的に部分的に切断されるためです。 [23]
ガイド付きツアーとベアリング [ 編集 | ソーステキストを編集します ]
ガイド付きツアーとベアリングは、機械コンポーネントの自由度の数を制限します。 RADOツアーにより、線形(翻訳者)軸の動き、丸いツアーまたはベアリングにより、回転が可能になり、波のガイドの場合、線形動きが可能になります。それらは、断面形状(スワローテールやVリードなど)と、磁気ベアリング、ローリングツアー、スライドガイドへのリーダーシップ分離のタイプに従って区別されます。ガイド付きツアーとベアリングは、摩擦値が少なく、低摩耗の影響を受け、振動を避けるための良好な減衰を受け、落下するチップや他の部品から保護され、できるだけ軽減され、メンテナンスが少なく、剛性が高いと言われています。 [24] [25] [26]
最も単純なバージョンは、2つの接触面が潤滑油で濡れている流体力学的ベアリングです。特定の最小速度からのみ、潤滑油の使用の摩擦削減効果があります(いわゆるスティックスリップ効果)。静水圧ベアリングでは、ポンプを使用して油圧が蓄積されます。これは、単独で接触面を分離します。空力ツアーでは、アッパーコンポーネントがエアクッションにスライドします。ほとんどのガイド付きツアーは、接触面が丸いボディ(主にボール)から分離されているローリングツアーとして実行されます。 [27] [28]
ドライブ [ 編集 | ソーステキストを編集します ]
ドライブユニットには、作業の動きを担当するメインドライブと、ツールの配置のためのフィードドライブが含まれます。冷却潤滑剤輸送、チップコンベア、または油圧の生成など、他のすべてのタスクのドライブは、補助ドライブと呼ばれます。ドライブの要件は、経済、高い最大速度、および大規模で継続的に調整可能な速度範囲に強く影響するため、高いダイナミクス(特に加速)です。 [29]
メインドライブ [ 編集 | ソーステキストを編集します ]

メインドライブは通常、モーター、トランスミッション、セキュリティカップリング(最も単純な場合は、過負荷の場合に滑るVベルト)、およびツールまたはワークピースのキャリアとしてのメインスピンドルで構成されています。他の工作機械には、電気モーターのローターがメインスピンドル(MotorSpindle)に直接収まる直接駆動があります。特にモチーフを使用する場合、ドライブの大規模なパフォーマンスを考慮して、フレームの熱膨張により機械の不正確さを避けるために、損失の損失を審議することが重要です。
力強いモーターは、主にモーター(同期または非同期)として使用されます。時折、DCモーターまたは油圧または空気圧エンジンも使用されます。トルク速度変換用のギアは、多くの場合、エンベロープギアや摩擦ギアなどの無限に可変のギアです。回転モーターの動きを翻訳の動きに変換するためのギアボックスは、ラック噴射システム、ボールスレッド操作、クランクギア、またはネジギアです。
隣接 [ 編集 | ソーステキストを編集します ]
今日、すべての可動軸には一般に、独自のフィードドライブがあります。それらはマシンの作業精度にとって非常に重要であるため、迅速かつ均一に実行し、ポジショニングの精度が高い必要があります。それらは、翻訳の動きを直接生成する線形直接ドライブに分割され、回転駆動型はギアによってのみ変換されます。通常、メインドライブと同じギアボックスが使用されます。追加のドライブは、ほぼ独占的に電気的です。油圧エンジンはめったに使用されません。 [30]
操舵 [ 編集 | ソーステキストを編集します ]
制御は工作機械を自動化するのに役立ちます。たとえば、コーナリングディスクを使用して、工作機械の初期コントロールが依然として機械的に実装されていました。今日、それらは電気的に操作されています。 B.リレーまたは半導体成分付き。工作機械の特別な制御は数値制御です。今日、彼らはほぼ望ましいワークピースの生産を可能にします。これには、プログラムされた列車に沿ってツールをリードする優れた鉄道コントロールが必要です。 [最初に30] [32]
電気制御 [ 編集 | ソーステキストを編集します ]
電気コントロールは、すべての信号を読み取ります(たとえば、オペレーターによって動作するボタンまたはスイッチを介して、温度、圧力、またはパスセンサーを介して)それらを処理し、制御セッター(例:エンジンまたはディスプレイディスプレイ)に信号を与えます。一方で、それらはプログラムされたコントロール(VPS)とストレージプログラム可能なコントロール(SPS)を接続し、他方ではリンクおよび排水制御への制御原則に従って分割されます。 VPSを使用すると、関数は個々のアセンブリ(リレー)の接続によって決定されます。特にセキュリティ批判的なアプリケーションの場合に使用されます。一方、PLCの場合、関数はメモリに保存されているソフトウェアによって決定されます。それらはほとんどの電気制御を構成し、通常はドライブを直接制御しますが、他のマシン(たとえば、通路など)と通信し、CNCコントロールにインターフェイスを提供することもできます。リンクコントロールの場合、出力信号は、入力信号の論理リンク(論理およびゲート、またはガター、非ガッター…)によって決定されます。たとえば、モーターを選択したり、フィードドライブを制御するために使用されます。一方、排水制御は徐々に処理を余儀なくされており、純粋なリンク制御よりも工作機械にとってはるかに重要です。 Zの世話をします。 B.ツールを変更する。 [33]
数値制御 [ 編集 | ソーステキストを編集します ]
数値制御(狭い:数値制御、ノースカロライナ州)は、電気よりもはるかに柔軟な工作機械の特別なコントロールです。それらは排水制御に属し、個々の排水ステップを英数字の形で示します。ポールストリップはもともとデータの入力に使用されていましたが、すぐにマイクロプロセッサテクノロジー(コンピューター化された数値制御、CNC)に切り替えられました。今日、両方の用語は実用的です。彼らの主なタスクは、形状のパスに沿ったツールの動きです。 NCコントロールを使用すると、同時に2つ以上の軸とツールzを制御することができます。 B.円形の経路を導く。これを行うために、コントロールは鉄道を小さなセクションに持ち込み、一方の手でこれらのセクションでポイントに乗っています。これらのポイント間のパスは補間されています。これにより、軸の宿泊値がドライブに渡されることを計算します。
プログラミングは、作業を準備することでオフィスで実行することができます。または、オペレーター(ワークショップ指向のプログラミング、WOP)がワークショップで直接実行できます。シミュレーションプログラムは、作業スペースでのツールの衝突を回避し、必要な旅行ルートとCADデータからの生産期間を独立して計算するのに役立ちます。このデータは、より高いレベルの生産計画および制御システムに渡すことができます。 CNCプログラムは、必要に応じて必要に応じて、個々のマシンに必要なプログラムを提供する中央リードコンピューターに保存することもできます(分散数値制御、DNC)。また、ツールの摩耗を計算し、機械の変形を部分的に補正するために、切削力を監視することもできます。
最新のCNCコントロールは、注文、パレット、ツール、サービスライフマネジメントを処理することもできます。 [34]
ツールメモリとチェンジャー [ 編集 | ソーステキストを編集します ]


工作機械には多くの場合、ツールストアが装備されており、そこからツールを直接置き換えることができます。ガードマシンには、多くの場合、必要なツールを変更しないが、作業レベルに変わるリボルバーがあります。最新の工作機械の場合、プログラムされたサービス寿命が終了した後、または実際のツール摩耗(スピンドルエンジンを介して測定された切断電力)に従って、提供された交換用ツールは独立して置換されるため、そのような機械は自動ワークチューチャーと組み合わせて機能します。 [35]
測定システム [ 編集 | ソーステキストを編集します ]
最新の工作機械には、状況zを記録するために使用される測定システムがあります。 B.ツールまたは車軸スライドを提供します。必要な角度と長さの測定値は、主に光電子です。 B.回転波の増分メーカーまたは絶対値プロバイダーと、ガラススケールを測定する位置の直接。さらに、オーム、誘導、容量性、磁気、または電磁原理が一般的です。 [36]
測定デバイスでは、直接および間接パス測定システムが区別されます。両方の測定システムで、カバーされているスケールセクションはセンサーを介してカウントされ、カバーされたパスはこの数値から計算されます。間接測定システムの場合、スケールは円内に配置されているため、システムはスレッドスピンドルの角度変化を測定し、糸の勾配上の動きの変化を計算します。より正確な直接パス測定システムを使用すると、スケールは動きの方向に平行に取り付けられているため、セクションの長さ(カウントされたセクションの数を掛けて)は、カバーされたパスに直接対応します。 [37] [38]
ツール録画 [ 編集 | ソーステキストを編集します ]
高精度でツールを迅速に変更するために、ツール記録(インターフェイスツールスピンドル)が標準化されています。過去には、回転ツールに使用されていたため、モールスコーン(MK)が回転するために使用されていました。技術的な利点により、今日の中空シャフトコーンが使用されています。 HSK録音などの場合内側の輪郭に張力をかけることは、システムが高速に適していることを意味します。すべての録音システムには、しばしば混合された機械公園で合理的なツールの使用を可能にするために、他のシステムにアダプターがあります。 [39]
ワークチェンジャー [ 編集 | ソーステキストを編集します ]
最新のミリング機と掘削機には、作業スペースと交互に持ち込むことができるワークピースを張力するための2つ以上のパレットがあることがよくあります。これにより、張力操作を作業スペースの外で実行できますが、前のパレットで処理が行われます。ワークピースが説明されているようにパレットに置き換えられた場合、パレットチェンジャーについて話します。大きなワークピースを切り替えてロボットに置き換えることができます。 [40]
購入および処分施設 [ 編集 | ソーステキストを編集します ]
チッピング生産の工作機械には、主に冷却潤滑装置が装備されています。これらは通常、機械のスプレーノズル、スピンドルヘッドのスプレーノズル、またはそれぞれのツールのノズルで、ツールの作業エリアに水オイルエマルジョンを促進します。クーラントは循環でろ過されます。ただし、環境および職場に優しい生産の過程で、いわゆる最小数量潤滑(MMSまたはMMK)がますます切り替えられています。空気を備えた非常に少量の冷却潤滑剤と活動点に噴霧されます。分離されたチップを作業スペースからコンテナに促進する供給コンベアには、供給施設と廃棄施設も含まれています。 [41]
機械の建物 [ 編集 | ソーステキストを編集します ]
通常、工作機械には機械のハウジングがあります。これは、オペレーターが飛んでいるチップ、冷却潤滑剤、結果として生じる騒音汚染、および可動部品の怪我に対する保護から、また保護から保護するのに役立ちます。大型の機械とシステムは、軽い障壁とグリッドによって保護されています。
安全コンポーネント [ 編集 | ソーステキストを編集します ]
工作機械はプロセス関連の危険を引き起こす可能性があるため、人々を保護する機能が形成されます。マシンのガイドラインによると、安全コンポーネントは、個別に配置された安全機能を確保するために使用されるコンポーネントであり、その障害および/または誤動作が人々の安全性を危険にさらすこと、およびマシン自体の機能に必要ではありません。安全コンポーネントは、4つの特性すべてを満たす必要があります。
安全コンポーネントの非網羅的なリストは、機械指令の付録Vにあります。
- 取り外し可能なジョイントシャフト用の保護装置
- 人の傾向のための保護装置。
- 付録IV番号9、10、および11に記載されている機械用のロックを備えた電力型可動式分離保護装置。
- セキュリティ機能を確保するためのロジック単位。
- 危険な機械の動きを制御するための追加の故障認識を備えたバルブ。
- マシンの排出を削除するシステム。
- 作業プロセスに直接関与している可動部品から人々を保護するために、分離および非分離保護装置。
- 課税の場合のヘッジと運動の制限のための施設。
- 座席の個人サポート施設。
- 緊急停止コマンドデバイス。
- 潜在的に危険な静電充電を防ぐ派生システム。
- 付録I番号1.5.7、3.4.7、および4.1.2.6に従って、エネルギー境界と救援装置。
- 騒音と振動排出を削減するためのシステムと施設。
- ロール保護構造(ROPS)。
- 落下物に対する保護構造(FOPS)。
- 2つのハンドされたサーキット。
- さまざまなレベル間の人々の取り込みおよび/または下向きの輸送のための機械の安全コンポーネント。 b。)負荷キャリアのクラッシュまたは制御されていない上向きの動きを防ぐファンデバイス。 c。)速度リミッター。 d。)非線形特性または返品減衰を備えたエネルギーストーリングバッファー。 e。)エネルギー消費バッファー。 f。)漁業装置として使用されている場合、主要な油圧円のシリンダー上の安全装置。 g。)電子部品を備えた安全回路の形の電気安全装置。
- 消火システム
等
パフォーマンス、旅行速度、ツールの変更時間など、工作機械の経済に影響を与えるプロパティに加えて、完了する製品の品質に影響を与えるプロパティもあります。これらは:
幾何学的精度 [ 編集 | ソーステキストを編集します ]
幾何学的精度は、無負荷マシンの製造品質、つまり処理力から負荷をかけないことを示します。 [42] 達成可能な幾何学的精度は、本質的に工作機械の製造品質、ゲーム、デザインから生じます。形状と位置の逸脱を区別します。
静的剛性 [ 編集 | ソーステキストを編集します ]
静的な剛性または剛性は、幾何学的な静的(壁の厚さ、交差セクション)および使用される材料の特性に起因します。さらに、ジョイントとガイド付きツアーの形状、形状、数(機械要素の固体および可動接続)は、達成可能な剛性に決定的です。静的変形は、CNC制御によって補償できます。
動的剛性 [ 編集 | ソーステキストを編集します ]
機械の動的な剛性は、しばしば振動を引き起こす多様な力の場合の変形に起因します。それらは、ワークピース(特に表面の慈悲)とマシンの寿命に悪影響を及ぼし、したがって一般的に望ましくありません。静的とは対照的に、動的変形は提案の頻度にも依存しますが、簡単に修正することはできません。自己制御と異物の振動を区別し、それが自由で強制振動に分割されます。 [43] [44]
1回の刺激は、自己周波数の頻度を持つ自由振動につながり、ゆっくりと沈静化します。
定期的に繰り返される提案の場合、提案の頻度との強制振動があります。これらは、不均衡(エンジンなど)、ギアボックスの歯の介入エラー、倉庫エラー、または摩耗ツールによって、基礎を介して機械に導入できます。
ゾンドリーの振動は、製造プロセス自体から発生します。その後、マシンは自己周波数でスイングしますが、時間とともにますますスイングします。これは、建物のボード、再生効果、または低下速度によって引き起こされる可能性があります。
熱挙動 [ 編集 | ソーステキストを編集します ]
工作機械の熱挙動は、温度変化、特にワークピースに対するツールの層の敷設に対する反応を説明しています。これは、熱源の作用と、熱の量とその位置または配置に応じて低下することに大きく影響されます。 [45] 熱負荷における内部の影響と外側の影響を区別します。内部の影響はzです。 B.ドライブエンジン、ポンプ、倉庫、ガイド付きツアー、油圧システムでのドライブ損失、またはツール、ワークピース、チップ、クーラントの熱を変換または保存することにより引き起こされます。外部の影響は、屋内気候(温度分布、温度変動、気流)、直接(一面)熱放射(太陽、暖房システム、隣接するシステム)、または暖房(基礎、目標と窓を通る新鮮な空気が流れる)を介して引き起こされます。
精度を向上させ、温度の変動を低く抑える努力にもかかわらず、熱相対的にマシンを構築することが利点です。熱対称性とは、拡張が相互にキャンセルすることを意味します。影響の成分における予想される温度分布、および長さと膨張係数。工作機械の温度挙動に関する知識により、CNC制御の熱膨張を部分的に補償することができます。
顧客やユーザーの観点から工作機械にさまざまな要件が作成されています。このマシンは、幾何学的精度と静的、動的、熱剛性に起因する、必要な作業精度に準拠することを目的としています。作業の精度は、機械容量による品質管理システムのコンテキストで説明されています。原則として、建設文書から生じる必要な製造精度よりも優れている必要があります。
工作機械の経済は、主にその生産性によるものです。前方時間、メイン時間、およびセットアップ時間を短縮することで増加させることができます。たとえば、加工センターや製造セルは、すでに処理のために他のツールやワークピースを準備しているため、鎧とサイドの時間を節約できます。主な時間は、主に切断速度の増加(チップの場合)の増加によって短縮されます。多くの製品のライフサイクルはマシンの寿命よりも短いため、より大きなスペクトルのワークピースを処理できるはずです。これには、ジオメトリと使用される材料の違いが含まれます。調達費用だけでなく、コストにとって重要であるだけでなく、運営および処分コストも重要です。総費用は、所有者とヒップアプローチの総コストで見積もられます。運用コストは、特定のエネルギー、ツール、および補助物質に起因します。 Gutenbergの生産機能により、Gutenbergの生産関数で特定の消費を最適化するモデルがあります。労働安全と環境保護のための最小要件は、法律によって規制されています。 [46]
企業の首都の大部分は工作機械に縛られています。調達のために、投資計算は実証済みの機器を提供します。コスト会計では、機械の使用は、機械の時間料金で製造することによって計算されます。プラント管理は機械の調達、保守、販売を扱っていますが、機械工学計画は最適な動作に関するものです。
ツールとワークの動きの組織と技術的実行は、工作機械またはロボットの運動学と呼ばれます。機械の構造に応じて、動きの方向は動き軸に分解されます。
連続運動学 [ 編集 | ソーステキストを編集します ]
連続運動学 運動系チェーンの古典的な構造について説明します。動きの軸の駆動のみを担当するアセンブリは、動きの異なる軸を備えた2秒になり、望ましい全体的な動きに到達するまでさらに接続できます。この運動学の特別なケースは、SO -Calledを提供します デカルト運動学 すべての供給軸は、デカルト座標系の座標を機械的な方法で実現するために、互いに垂直に配置されます。ほとんどの場合、すべてのフィードアクスルは、対応する座標軸に基づいています(たとえば、3次元で バツ 、 と と と )名前。
コンソールフライス機の例: マシンスタンドでは、スピンドルハウジングが動き、スイベルヘッドがフロントで粉砕ツールのキャリアとして成長し、機械軸のガイド付きツアーで と 。クランプテーブルは、マシン軸のコンソールを左右に移動します バツ 。コンソールは、マシンスタンドのクランプテーブルで上下に移動し、マシン軸を形成します と 。
Parallelinematics [ 編集 | ソーステキストを編集します ]
一 Parallelinematics 平行な動き軸を持つ運動学について説明します。これにより、ドライブが次のドライブを移動する必要がないことが回避されます。ここでは、平行なスティックキンマティクスがよく使用されます。
工作機械の研究プロジェクトの実装は、有望な幾何学的特性により、20年以上にわたって工作機械の研究プロジェクトに焦点を当てています。しかし、これまでに、生産における重要な使用は、伝統的に連続運動学を持つ機械によって支配されていました。並列映画の利点は、通常、管理要素の小さな質量により、より高い動的であり、これはすべてのガイド要素の負荷を均等に分割します。
(平行)stabkinematics [ 編集 | ソーステキストを編集します ]

連続運動学とは反対に、(並行)人員配置の運動学は、室内の定義された固定点に対する可動オブジェクト(ツール)の距離の変化に取り組んでいます。可動オブジェクトの空間位置(および場所)は、ベクトルベースの座標系(つまり、ゼロポイントとゼロポイントに基づいていません。 n の動きに関する平行ベクターではありません n 寸法をコードするには)、しかし、オブジェクトスペースポイントペア間の距離に基づいています。
通常、たとえば、純粋な位置の場合(回転軸のない)部屋に含まれています n 寸法 n + 1 距離情報も n + 1 明確な空間点が必要です。ただし、実際には、機械の設計は、多くの場合、理論的にアクセス可能なスペースの一部を除外しますが、これはしばしばのみです。 n 距離情報も n 不利な位置にポイントが必要です。たとえば、3人の貧困層のみを持つSo -Coldedの三脚は、3次元空間の事前定義された領域に簡単に到達できます。
したがって、正確な位置決めは、複数の望遠鏡アームの長さの変化を介して達成されます。これらはすべて、一緒にイモビングし、もう一方の端にオブジェクトを配置する位置に固定されています。
例:ヘキサポデン [ 編集 | ソーステキストを編集します ]
SO -CALLED HEXAPODS(Hexa Greek Numbers: 六 、Griechの下で。 フット )部屋のツールの目的の動きを作成し、同時にツールの吸収またはツールの望ましい傾向を作成するために、並列回路で同時に互いに作業します。
専門文学 [ 編集 | ソーステキストを編集します ]
- Claus-jeault conrad: 工作機械のペーパーバック。 Fachbuchverlag Leipzig、ミュンヘン/ウィーン2002、ISBN 3-446-21859-9。
- アンドレアス・ハーシュ: 工作機械:基本、解釈、実行の例。 第2版。 Springer-Vieweg、Wiesbaden 2012、ISBN 978-3-8348-0823-3。
- reimund neugebauer(ed。): 工作機械:チップの構造、機能、適用、および工作機械の取り外し。 Springer、Berlin/ Heidelberg 2012、ISBN 978-3-642-30077-6。
- ハンス・カート・テンショフ: 工作機械:基本。 Springer Textbook、1995、ISBN 3-540-58674-1。
- マンフレッド・ウェック、クリスチャン・ブレチャー: 工作機械 。
- バンド1: マシンの種類とアプリケーションの領域。 6.エディション。 Springer、Berlin 2005、ISBN 3-540-22504-8。
- バンド2: 建設と計算。 8.エディション。 Springer、Berlin/ Heidelberg 2005、ISBN 3-540-22502-1。
- バンド3: メカトロニクスシステム、フィードドライブ、プロセス診断。 6.エディション。 Springer、Berlin/ Heidelberg 2006、ISBN 3-540-22506-4。
- バンド4: 機械とシステムの自動化。 6.エディション。 Springer、Berlin/ Heidelberg 2006、ISBN 3-540-22507-2。
- バンド5: 測定検査と評価。 第7版。 Springer、Berlin/ Heidelberg 2006、ISBN 3-540-22505-6。
辞書 [ 編集 | ソーステキストを編集します ]
- ヘンリー・ジョージ・フリーマン: 星の工作機械 – ドイツ語 – 英語の用語とコメント。 Poliginm W. Girardet、Eating 1973、ISBN 3-7736-5082-5。
- Hans-Dieter Junge: 工作機械と機械工学の辞書:英語 /ドイツ語、ドイツ語 /英語 – 辞書工作機械と機械生産。 Weinheim 1992、ISBN 3-527-27993-8。
工作機械の歴史に関する本 [ 編集 | ソーステキストを編集します ]
- GünterSpur: 工業界の変化から、製造技術の文化的な歴史的見解である工作機械まで。 カール・ハンサー・ヴェルラグ、ミュンヘン/ウィーン1991、ISBN 3-446-16242-9。
- W.スティーズ: 工作機械の歴史1700〜1910。 オックスフォード1969、OCLC 476608011 。
- ↑ reimund neugebauer(ed。): 工作機械:チップの構造、機能、適用、および工作機械の取り外し。 Springer、2012、S。4。
- ↑ H. K.Tönshoff: 工作機械。 Springer、Berlin 1995、S。2。
- ↑ H. K.Tönshoff: 工作機械。 Springer、Berlin 1995、S。1f。
- ↑ アンドレアス・ハーシュ: 工作機械:基本、解釈、実行の例。 第2版。 Springer-Vieweg、Wiesbaden 2012、ISBN 978-3-8348-0823-3、p。2。
- ↑ GünterSpur: 工業界の変化から工作機械を通して。 Carl Hanser Verlag、Munich/ Vienna 1991、ISBN 3-446-16242-9、pp。25–95。
- ↑ GünterSpur: 変化における生産技術。 1979、S。116F– 118、64–89。
- ↑ GünterSpur: 変化における生産技術。 1979、S。116–138。
- ↑ GünterSpur: 変化における生産技術。 1979、S。140、176–183。
- ↑ GünterSpur: 工業界の変化から工作機械を通して。 Carl Hanser Verlag、ミュンヘン/ウィーン1991、ISBN 3-446-16242-9、pp。313–330、424–430。
- ↑ Hans-JürgenWarnecke: フラクタルメイク。 Springer、1992、ISBN 3-540-55200-6、S。14–19。
- ↑ H. K.Tönshoff: 工作機械。 1995、S。3。
- ↑ M.ウェック、C。ブリーチャー: 工作機械。 第5版。第1巻、1998年、p。3。
- ↑ ツール +マシン。 2015年1月、p。11。 onlinearchiv ( 記念 2015年6月13日から インターネットアーカイブ ))
- ↑ reimund neugebauer(ed。): 工作機械:チップの構造、機能、適用、および工作機械の取り外し。 Springer、2012、S。18f。
- ↑ M.ウェック、C。ブリーチャー: 工作機械。 第5版。第1巻、p。17。
- ↑ M.ウェック、C。ブリーチャー: 工作機械。 第5版。第1巻、51〜53ページ。
- ↑ A.ハーシュ: 工作機械。 Springer Vieweg、Wiesbaden 2000、p。412。
- ↑ reimund neugebauer(ed。): 工作機械:チップの構造、機能、適用、および工作機械の取り外し。 Springer、2012、S。16f。
- ↑ A.ハーシュ: 工作機械。 Springer Vieweg、Wiesbaden 2000、p。83。
- ↑ M.ウェック、C。ブリーチャー: 工作機械。 バンド2: 建設と計算。 8.エディション。 Springer、Berlin/ Heidelberg 2005、pp。7–12。
- ↑ A.ハーシュ: 工作機械。 Springer Vieweg、Wiesbaden 2000、pp。86–88。
- ↑ テーブルから取られたテーブル:R。Neugebauer: 工作機械。 2012年、S。423。
- ↑ M.ウェック、C。ブリーチャー: 工作機械。 バンド2、S。183–210。
- ↑ W.バーマン: 工作機械コンパクト – アセンブリ、使用、トレンド。 21.エディション。 Springer、Berlin 2013、p。65。
- ↑ A.ハーシュ: 工作機械。 Springer Vieweg、Wiesbaden 2000、pp。97f。
- ↑ reimund neugebauer(ed。): 工作機械:チップの構造、機能、適用、および工作機械の取り外し。 Springer、2012、S。381f。
- ↑ M.ウェック、C。ブリーチャー: 工作機械。 バンド2、S。234–487。
- ↑ J.ミルバーグ: 工作機械 – 基本。 第2版。 Springer、Berlin 1995、pp。153–226。
- ↑ W.バーマン: 工作機械コンパクト – アセンブリ、使用、トレンド。 21.エディション。 Springer、Berlin 2013、pp。36f。
- ↑ H. K.Tönshoff: 工作機械。 Springer、Berlin 1995、S。125–162。
- ↑ M.ウェック、C。ブリーチャー: 工作機械。 バンド3: メカトロニクスシステム、フィードドライブ、プロセス診断。 第5版。 Springer、Berlin/ Heidelberg 2001、pp。33–57、113–318。
- ↑ J.ミルバーグ: 工作機械 – 基本。 第2版。 Springer、Berlin 1995、pp。329–370。
- ↑ M.ウェック、C。ブリーチャー: 工作機械。 6.エディション。第3巻、pp。99–110。
- ↑ M.ウェック、C。ブリーチャー: 工作機械。 6.エディション。第4巻、pp。151–182。
- ↑ M.ウェック、C。ブリーチャー: 工作機械。 第5版。第1巻、Springer、1998、pp。494–533。
- ↑ M.ウェック、C。ブリーチャー: 工作機械。 バンド3: メカトロニクスシステム、フィードドライブ、プロセス診断。 第5版。 Springer、Berlin/ Heidelberg 2001、pp。40–88。
- ↑ H. K.Tönshoff: 工作機械。 Springer、Berlin 1995、S。220–233。
- ↑ J.ミルバーグ: 工作機械 – 基本。 第2版。 Springer、Berlin 1995、pp。318–322。
- ↑ M.ウェック、C。ブリーチャー: 工作機械。 第5版。第1巻、Springer、1998、pp。494–533。
- ↑ M.ウェック、C。ブリーチャー: 工作機械。 第5版。第1巻、Springer、1998、pp。533–569。
- ↑ M.ウェック、C。ブリーチャー: 工作機械。 バンド2、S。607–631。
- ↑ A.ハーシュ: 工作機械。 Springer Vieweg、Wiesbaden 2000、p。56。
- ↑ ルドルフジュルグラー: マシンダイナミクス。 3.エディション。 Springer、Berlin 2004。
- ↑ J.ミルバーグ: 工作機械 – 基本。 第2版。 Springer、Berlin 1995、pp。79–112。
- ↑ M.ウェック、C。ブリーチャー: 工作機械。 バンド2: 建設と計算。 8.エディション。 Springer、Berlin/ Heidelberg 2005、pp。84–95。
- ↑ W.バーマン: 工作機械コンパクト – アセンブリ、使用、トレンド。 21.エディション。 Springer、Berlin 2013、pp。1–5。
Recent Comments